Restoration project: FGK Morris restoration part 3
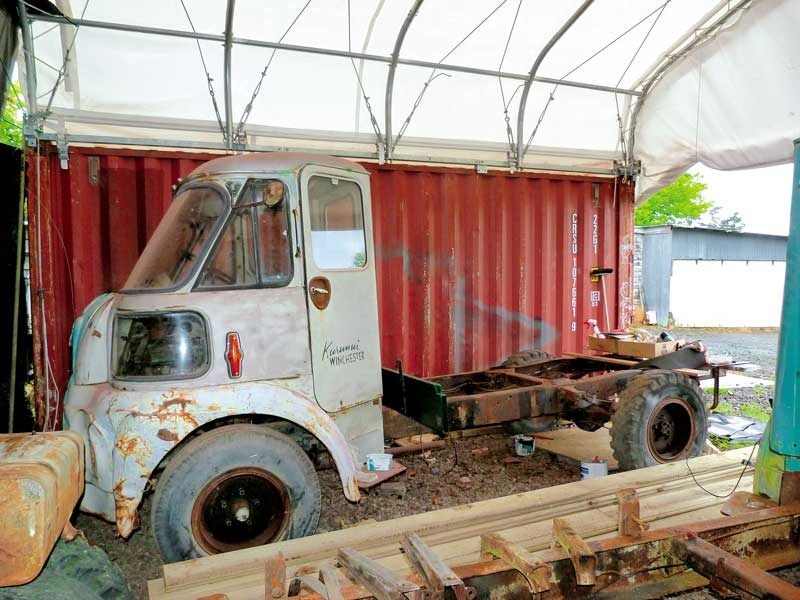
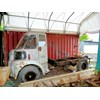
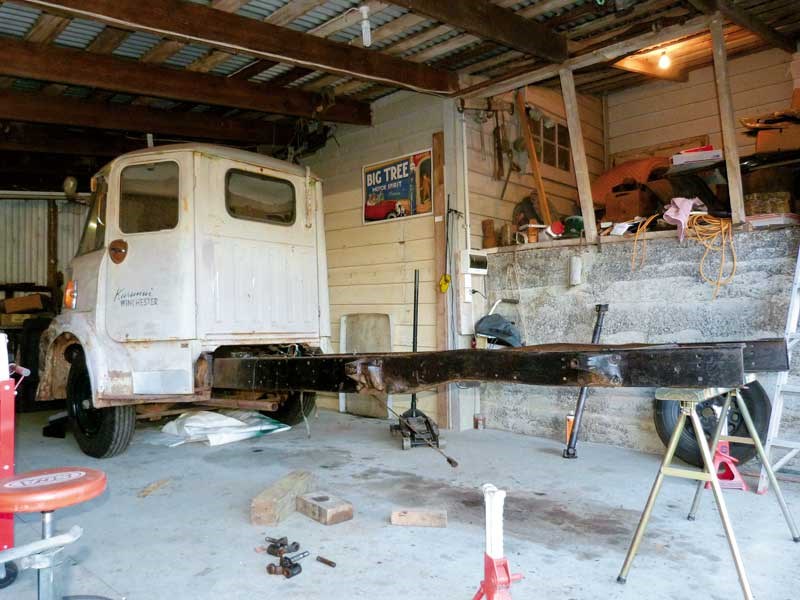
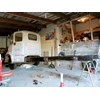
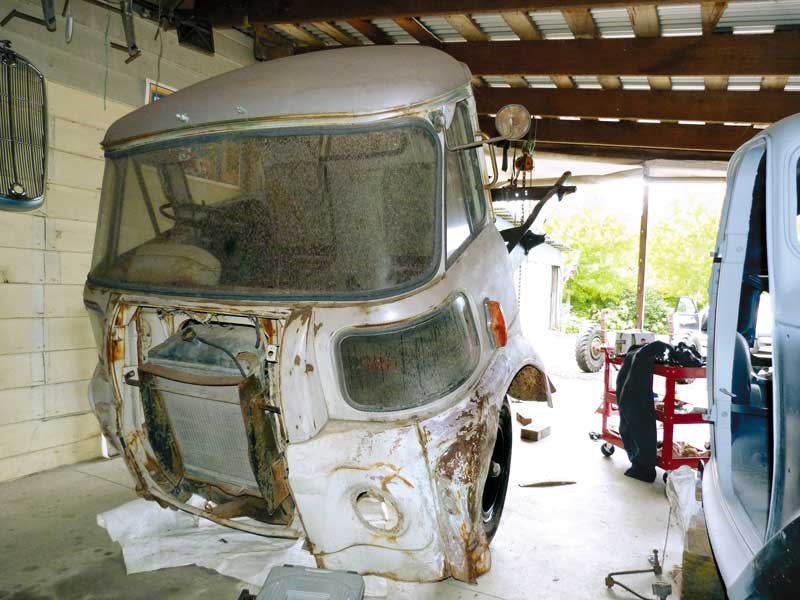
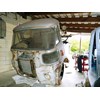
![]() |
![]() |
![]() |
Lyndsay Whittle continues his project on the FGK Morris in part 3 of this series
It appears that I have a bit of swift catching up to do if I’m going to make this project fly in any shape or form, as
I have already mentioned in last month’s issue that getting under way with the project has been thwarted to some extent by the fact that a couple of other restorations have gotten in the way over the past year and a bit. Anyway, on with the story.
The steel-framed deck, which needed to be removed to get at the chassis for cleaning purposes turned out to be an unwieldy affair, as it was welded directly to the chassis and not mounted in the traditional way by means of U-shaped bolts or threaded rod and steel top and bottom plates.
On first inspection, I was mildly afraid of what I might find post-removal of the deck, as I’ve seen trucks in the past with cracked chassis caused by the lack of flexion allowed as a result of the direct welding method being employed.
However, once the deck was off, a decent water blast revealed that there were no cracks, and I could only conclude that because the truck had always been used on sealed township environment and not on rough country roads or farmer’s paddocks, it had had a rather quiet life.
In any event, whatever the reason, I’d dodged a bullet on this occasion and the chassis was in surprisingly good nick.
In fact, the old saying that if a job is going really well without any hitches along the way, you should be worried, was foremost in my mind as I sped along the road of restoration with considerable ease.
Anyway, I knew that I needed a stockpile of good luck in reserve for when the time finally comes to getting a VIN number. I know that bit won’t be easy!
But for the meantime, I’ll consider myself safe in knowing that the VIN part of the process is still a way off yet.
Call it burying my head in the sand if you will, but for the moment that’s all I need to egg myself on.
Having removed the deck and given the truck a good-old water blast, my thoughts turned to the next part of the process, which was to attend the worn rear spring shackle pins, some of which were so flogged out that there was about 20mm play on both the right- and left-hand springs. There is always an up and a downside to finding problems that you were hoping didn’t exist, and the worn shackle pins were no exception to the rule.
While I would have been pleased if all the spring hangers needed were to have some grease pumped into them, being as lazy as I am, I just know that I would have been happy to leave the diff in place and clean around it as best I could.
But now that I’d resigned myself to the fact that the diff was going to have to come out, I knew I was going to end up with a far tidier finished product, albeit at a much greater expense.
I knew it wasn’t going to be cheap, as spare parts for FGK Morris trucks are not as easy to source as any model of Bedford I’ve owned, and I realised I’d have to have the shackle pins and bushes manufactured from scratch.
So the next job was to start taking the diff out and hoist the rear part of the truck up on a chain block and get to work scraping half a century of gunk of the old girl while the suspension hardware was being manufactured.
I took the sample parts into an engineering firm in Avondale who told me they could do the job but could neither give me a quote nor a timeframe for getting the job done. However, they did say that they’d get onto it ASAP.
I had plenty of things to get on with back at the coalface anyway, so I left the sample parts with Rex the engineer and went back to work cleaning, grinding, and painting.
Sometimes I’m right, sometimes I’m wrong!
While I have to admit that this balance of right versus wrong is usually skewed in favour of the negative to a ratio of 90 percent, on this occasion, it turned out that I had a 50/50 marking on the shackle pin manufacturing score.
As I said previously, I’d figured the job was going to be expensive. I had also imagined that I wasn’t going to get a call from the engineers saying that the parts would be ready anytime soon. However, I was wrong on this score because it only took about a week before I got the call to come and collect my bits.
Engineer Rex said that they weren’t particularly busy at the time and that he was able to get his head engineer Dean onto it sooner than he’d originally thought.
Knowing that I’m usually wrong 90 percent of the time, I waited with baited breath for the next sentence in the conversation to hear if I would be wrong on the cost part of the equation.
I think I can safely leave it to your imagination as to whether I was right or wrong on this occasion.
There’s an old adage that good work isn’t cheap and cheap work isn’t good. This proved to be correct with the shackle pins and bushes, too, as when it was time to fit it all back on the truck, it all slid together with particular ease, thanks to Dean’s engineering prowess.
Back in the workshop, I was cracking on with the restoration to the point where the truck was back on four wheels, for the meantime at least, and I was thinking about turning it around and starting from the front and working my way back to the middle.
I’d being eyeing the engine up with the view to having a go at starting it up, but any thoughts of that had to be put on the back burner, as some work had come in for my previous restoration, the 1991 Mitsubishi transporter.
After all, something has to fund this restoration hobby, so off to work it was.
Having a go at starting the old girl up to hear if the weird old FGK would need an engine job was going to have to wait another few weeks longer.
Keep up to date in the industry by signing up to Deals on Wheels' free newsletter or liking us on Facebook.