Product profile: Dando Terrier Mini Rig
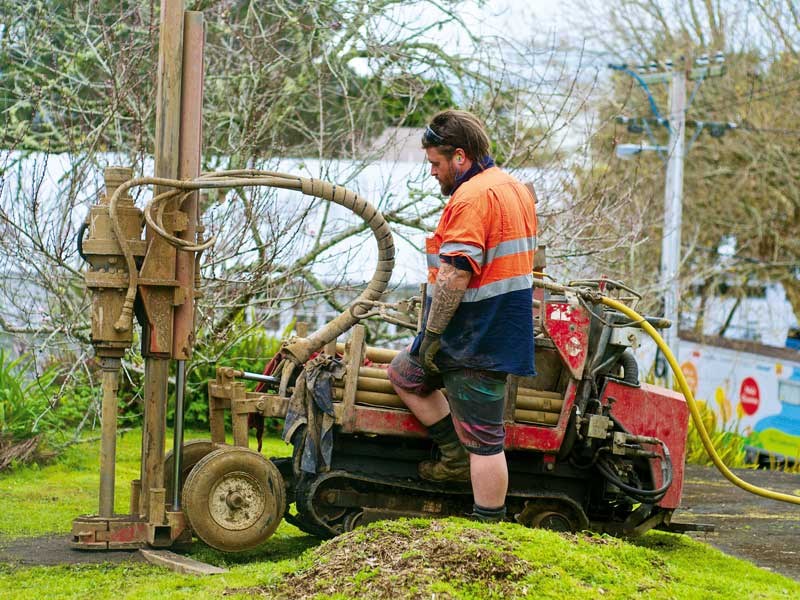
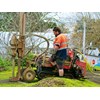
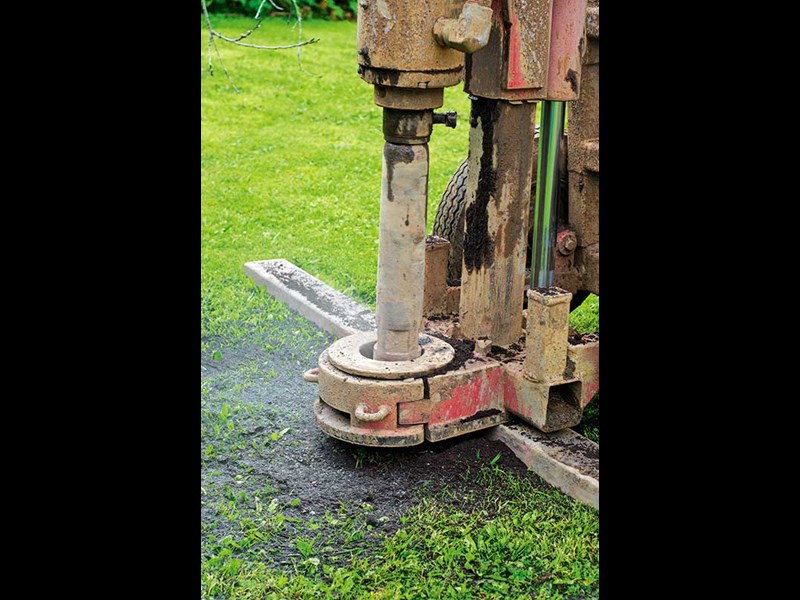
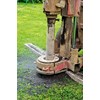
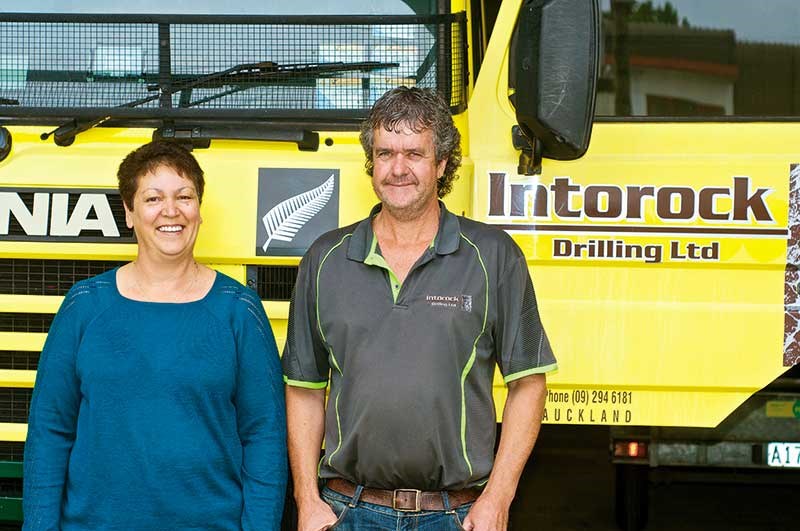
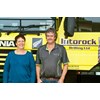
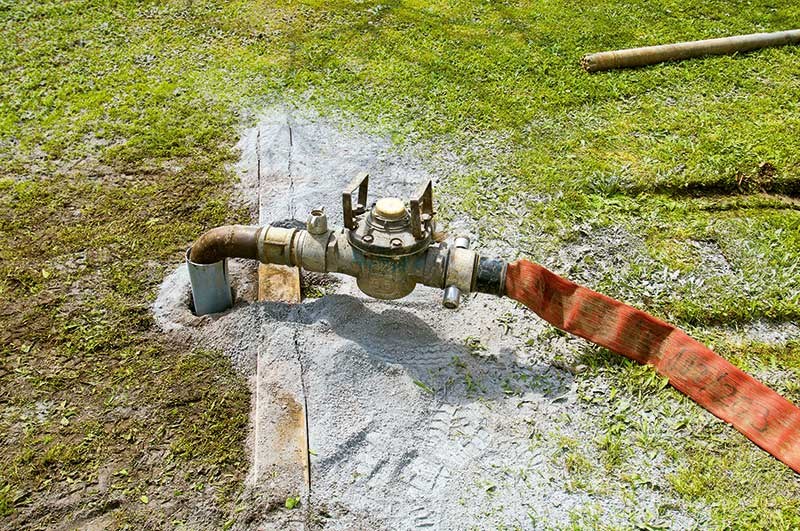
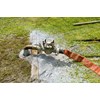
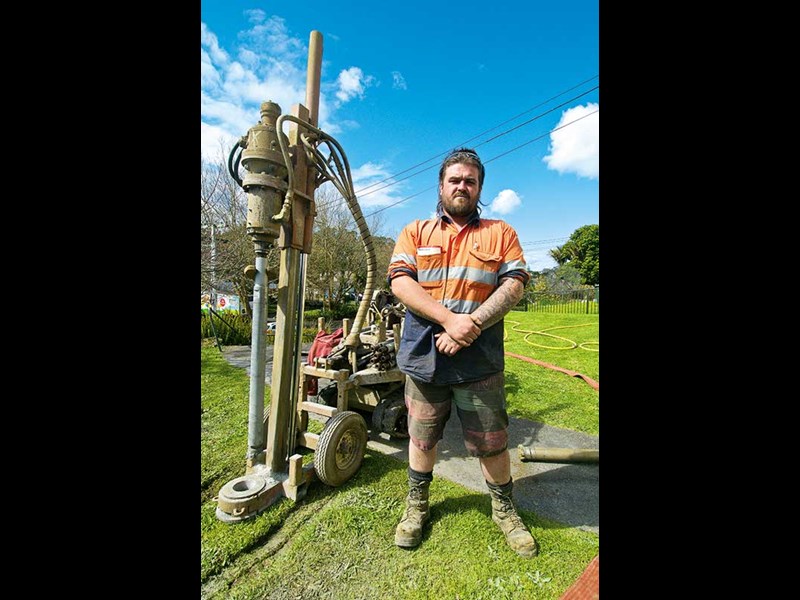
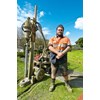
![]() |
![]() |
![]() |
Eliza and Ian Shaw from Intorock Drilling Ltd
|
![]() |
![]() |
Kieran Waite
|
As a result of some residential additions, a friend of mine required a new storm-water solution for his house. A new bore for soakage was chosen as the answer.
The house is located in central Auckland on an elevated site, and if you made a line joining Mt Eden, Mt St John and One Tree Hill, it would fall within that triangle. Knowing the property well, I was well aware that the topsoil (if you can call it that) is only around 300mm thick.
Below this is a solid slab of basalt rock, which is believed to be the remains of a lava flow when Three Kings erupted sometime earlier. Three Kings is now a large hole in the ground, having been mined for scoria for many decades since the eruption. Looking at the rear of the road-level garage, exposed a large wall of solid basalt, with a few fractures breaking the slab into layers. However, access was going to be the biggest issue for this job.
Intorock Drilling Ltd is a family-run business based in South Auckland that employs six staff. As the name suggests, they drill into rock; like some other outfits that provide drilling services. However, Intorock only drills rock, nothing else. It is the only construction rock drilling company around. With over 20 years’ experience, it runs four machines with matching compressors. Its largest is a monster that includes a self-contained cab. This machine is ideal for production drilling where many holes are needed in a row. The go-to unit is an Atlas Copco Airroc D40 from Sweden, and only few months old. However this unit has a width of 1900mm, which for this site, was too wide.
The fall-back machine, when access is tight, is a 2002 Dando Terrier Mini Rig. At 800mm wide it would easily fit down the 1700mm-wide side access. With a drilling depth of 20 metres, this machine would do the job nicely.
On drill day, the Dando was unloaded and driven from the rear of the site, down the narrow side alley, to the front of the section. Once a suitable point had been decided, it was time to set the unit up. A metal bar is placed on the ground to help distribute the weight and stop the drill head from sinking into the ground. This is a down-the-hole hammer machine, which means the first attachment is the drill and hammer unit. The hammer is operated via compressor air and is forced down into the ground by adding one-metre drill rods as it makes its way downward.
Being a soak bore, there was a requirement that it had to have a plastic lining to a depth of at least three metres under the surface, assuming that you had hit solid rock by that stage. If not, then you must continue drilling down until you find it. If the plastic lining finishes in loose small stones, there is a chance that the bore may collapse inside below this point and become blocked. Therefore, you drill until you can place the lining into solid rock. Then you continue down to find a fracture within the rock itself. The bigger the fracture, the more water it would be able to take in and because this is a soak hole, bigger is better. The question was, how deep did we need to go for this site?
Working a drilling machine is both a skill and an art. The operator will watch the trailings to get an idea of what type of rock the hammer is working through, and listen to the sound of both the compressed air and the engine revs. They will also be feeling the feedback on the controls as the hammer finds fracture and cavities under the surface.
Kieran Waite was the operator today, and coincidently, only a few months earlier, he had been drilling a hole just 100 metres down the road for the local council. There, he had found mostly clay but here, within eyeshot of that site, it was clearly basalt rock – and lots of it. So much so that the site was six metres above the road level. This was going to be an interesting drill.
As expected, the first 300mm was dirt that quickly enough became saucepan-sized rocks or smaller. Being loose material, the hammer would often jerk violently back and forth as the hammer worked its way through. At the three-metre mark, it was still loose rock, so deeper the hammer went. Just after five metres deep, we hit good rock and removed the drill so the plastic lining could be installed. Once this was tapped into place, the machine was moved back over the bore and a smaller hammer was then lower into the plastic pipe.
Now it was just a question of how far down the first fracture was. The plan was then to remove the drill and test how much water the new bore could take in. This step is to basically place a fire hose from the nearest fire hydrant and open the valve slowly while using a gauge to measure how much water is passing through the hose and into the bore. The water usually flows for around 15 minutes to confirm that there is ample absorption and the water does not back flow out the top.
At the 12-metre point, the flushed out trailings were starting to give indications that there could be a fracture soon. It was dark in colour and showed signs of water absorption. This was good news as there was a possibility that if the drilling was short in duration, this could result in a smaller than expected bill. But it was not to be. The colour started to change to a light grey, which meant dry rock and it stayed this way all the way down to the maximum depth of 20 metres.
Not being able to go deeper it was time to test what capacity the bore could take in. It had to be at least nine litres per second to replicate those once-in-a-decade downpours that seem to happen more often every year. If it couldn’t then another bore would have to be drilled to help the first bore achieve this, with the bill doubling if this was the case.
With fingers crossed, the valve was opened and after 15 minutes, the results came back at 13.4 litres per second. Success!
For the latest news and reviews, subscribe to Deals On Wheels magazine here.
Keep up to date in the industry by signing up to Deals on Wheels' free newsletter or liking us on Facebook.