1942 International fire truck restoration: part 3
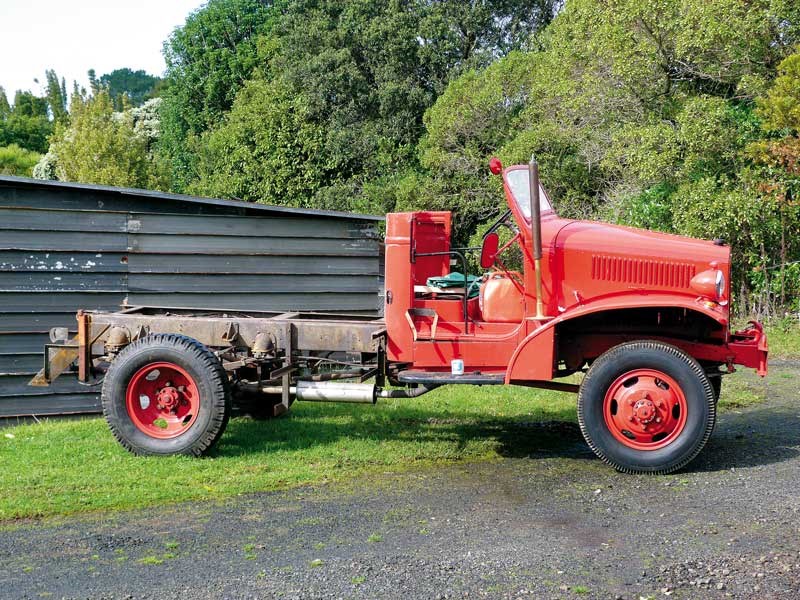
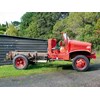
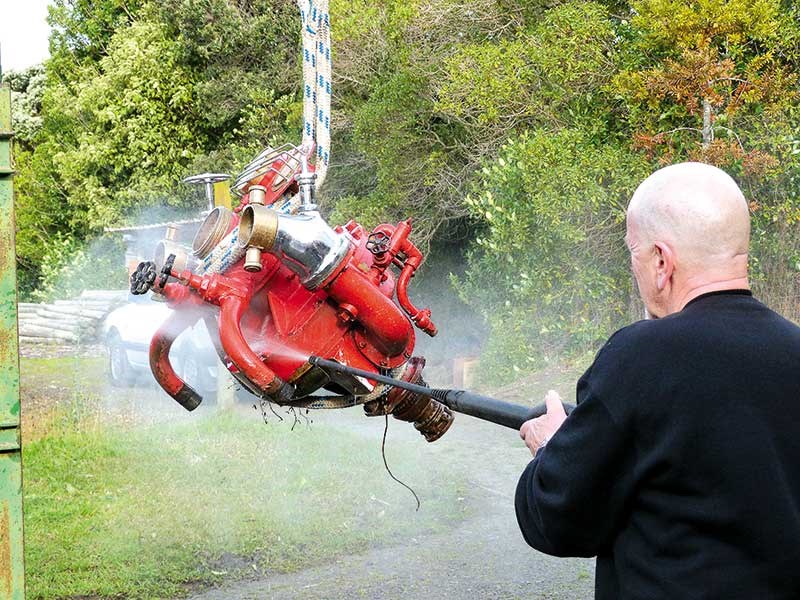
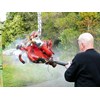
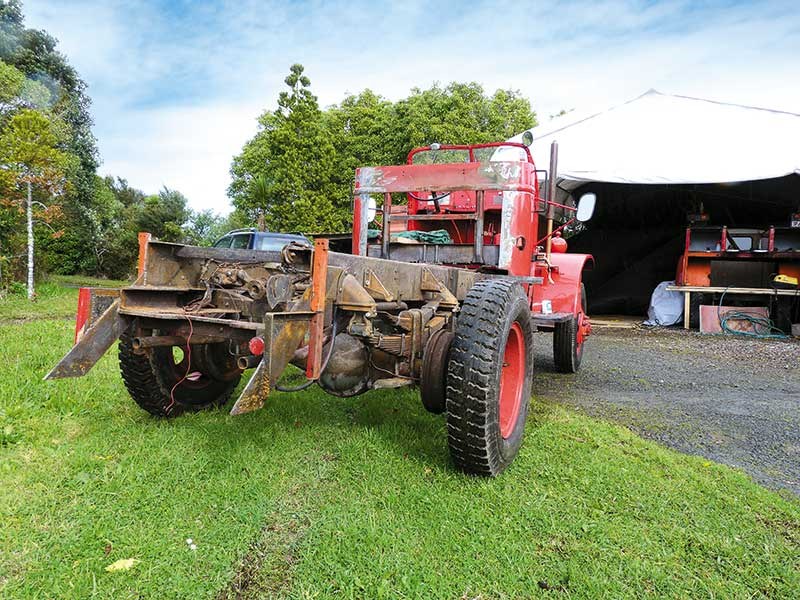
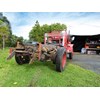
![]() |
![]() |
![]() |
The latest chapter in the story of Lyndsay Whittle restoring a 1942 International fire truck.
When I was screaming down Piha Road 40-odd years ago, sometimes standing on the back, sometimes as the driver, I’d have never dreamed that one day in 2015 I’d be restoring the old machine.
Back in the early ’70s when the truck was in its final years of operational life, as a 30-year-old, it seemed ancient at the time.
However, to put things into perspective, the current appliance at our station is a 1993 Mitsubishi, which makes it 22 going on 23, adding weight to the old saying that some things never change.
It’s fair to say that I have had a bit of interaction with the old truck in the intervening years between the time I used it as an operational vehicle and the current restoration.
I recall driving it in one or two Christmas parades in about 2005 and I had a little bit to do with making a film called Isaiah’s Fire back in 1999 in which the International was filmed in the opening sequence responding to a call to a dunny on fire down a dusty road.
It’s worth noting that the man who commissioned the restoration, Titirangi VFB deputy chief Evan Taylor played the role of a retired colonel in the film and those who have been following the story will have noticed that the name seems to have stuck.
Anyway I digress…
Our small restoration team consisting of engineer Dean Southey, Murray Firth and me were feeling pretty pleased with ourselves having got off to a flying start by removing the 400-gallon water tank as the first part of the process.
The removal of the tank allowed us to climb in behind the cab and in between the chassis rails to get a better idea of how the locker module could be removed.
By undoing a number of visible bolts it looked like removing the front mountings would be fairly easy, however it was to be a different story further to the rear of the machine.
I have to admit that had I have been doing the job by myself, at this point in the procedure I’d have felt like giving it up as a bad job.
However, Southey’s got big… I mean… Southey’s not one to walk away from a challenge, so by taking a leap of faith and grinding off what couldn’t be undone with a spanner, we were able to call upon ex Titirangi FB chief Gordon Latham with his Hiab to lift the pod off.
This whole removal process sounds simple enough, however all the pipework that connects the rear-mounted pump to the forward-mounted tank had been modified over the years to accommodate further pipework to supply cooled water to the radiator for when the machine was pumping at an incident.
Also there was a wiring loom which supplies power from a connection at the rear of the truck that supplies power to an element in the radiator.
It was revealed during the craning-off process that these needed to be disconnected at several anchor points along the way.
The removal of this paraphernalia of course added time and a degree of frustration to the job at hand, proof positive of the ‘no free lunch’ adage.
Anyway it all made for interesting work and eventually the module was sitting on the back of a nearby FG Morris truck which is also awaiting restoration.
The third stage of dismantling was the removal of the centrifugal pump and its expeller pump which all happened fairly quickly and without incident.
Now that a bare chassis was revealed we set about deciding how we were going to clean the chassis.
We discussed whether we would bead blast, use water jetting or even maybe do it the slow way with wire brushes and disc grinders.
Water jetting won the day, so we commissioned Aquamax to do the job.
The water jetting process uses water pressures of between 30,000 and 40,000psi and produced a result which was far superior to anything we could have achieved with the wire brush method.
Not only did it do a superior job but it completed the task in a fraction of the time it would have taken our team to prepare the chassis for painting.
The weather was diabolical on the day Aquamax arrived and it was difficult for onlookers to decipher which was mist from the water jetting and what was rain been driven horizontally by the howling gale.
In any event once the truck was placed back under cover, it took less than half an hour to blow any residual water off with compressed air and the chassis was able to be given a coat of etch primer the very next day.
All that remains now is to start putting all the components back together. These have been worked on in parallel with the work being undertaken on the cab and chassis.
Currently the three lengths of suction hose that are mounted on the left-hand side of the truck are being replaced by suppliers PSL Fire and Safety who are to refit the original brass screw couplings to the new hose.
Note: Suction hose is carried on fire appliances in order to draft water from an open source such as a pond, stream or water tank.
Brass waterway equipment is being polished by Terei Brothers in Waikumete in West Auckland who are also doing the chrome plating.
For the latest news and reviews, subscribe to Deals On Wheels magazine here.
Keep up to date in the industry by signing up to Deals on Wheels' free newsletter or liking us on Facebook.