Profile: Ian Howe Concrete Pumps
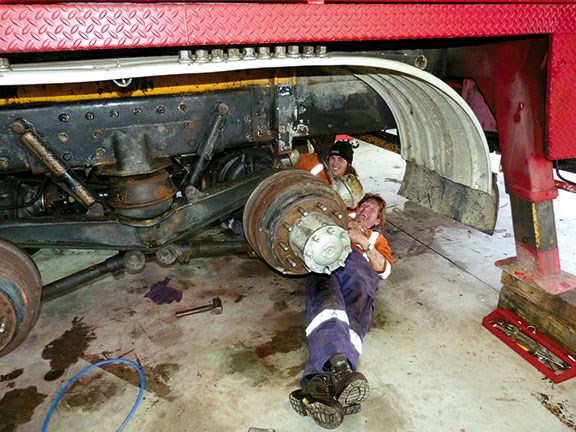
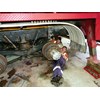
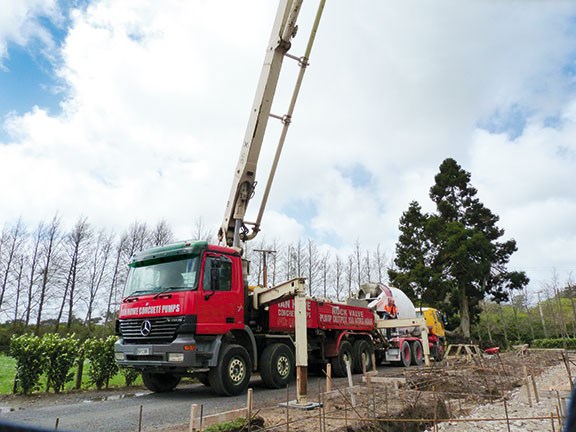
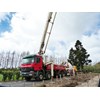
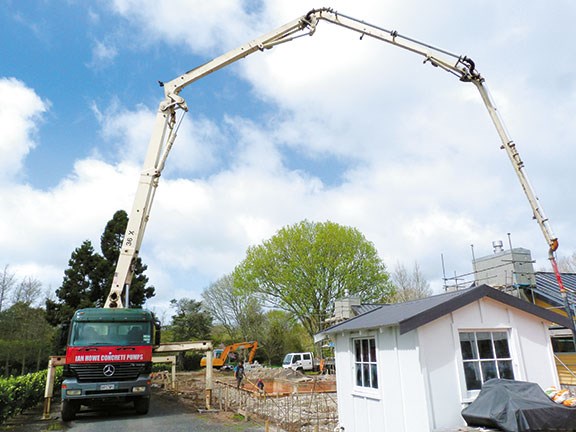
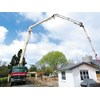
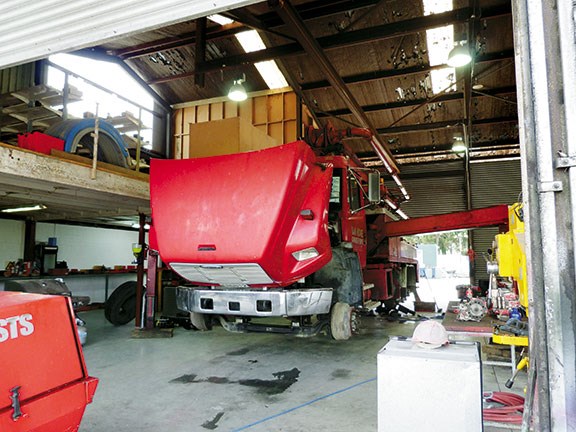
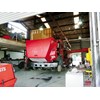
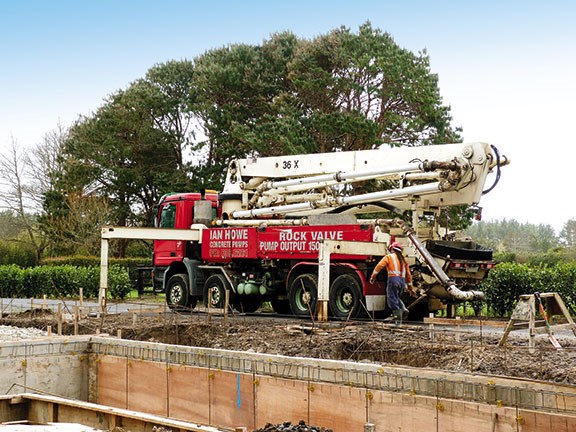
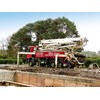
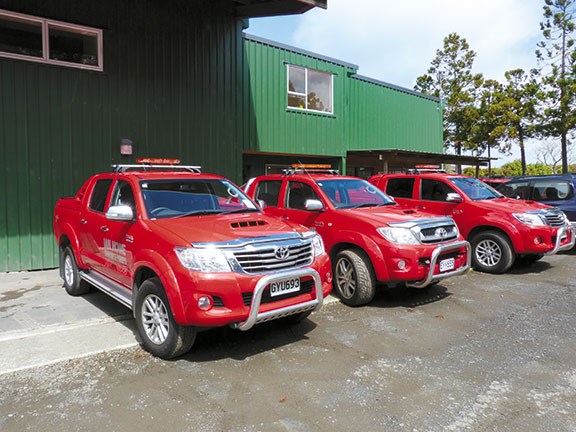
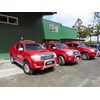
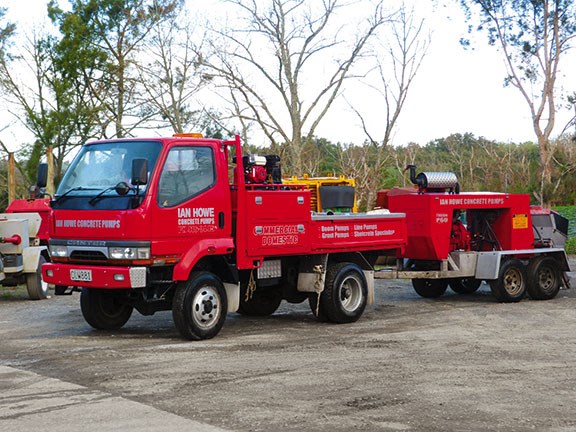
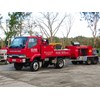
![]() |
Trent Howe and Johnny ‘Redline’ having fun working on a rear suspension
|
![]() |
The Actros in action on one of those ‘smaller’ domestic sites
|
![]() |
The 36m boom on the Actros reaching out on a footing job
|
![]() |
A Freightliner boom-pump being given a ‘birthday’ in the Howe workshop
|
![]() |
Preparing for an afternoon pour
|
![]() |
![]() |
Many a business has grown from what is commonly known as a ‘one-man band’, to become the pre-eminent business in its field — Ian Howe Concrete Pumps is one of them.
![]() |
Know-Howe
|
Ian Howe and partner Harriet Wells have devoted their adult lives to building an enterprise — the services of which are always in demand when concrete has to be moved from point A to point B on the building site.
Having moved down to Auckland from 'up north' back in the late 1970s, Ian got a job with a company that, at the time, was the largest concrete pumping firm in the North Island. When the company was bought out by a giant corporate-construction company he decided to make a go of it for himself and bought his first line-pump, which he towed behind a Land Cruiser.
Fast-forward to 2013 and Ian Howe Concrete Pumps has one of the largest fleets of line and boom pumps in Auckland.
For the past several years, commuters returning home from work on Auckland's north-western motorway wouldn't have been able to miss the impressive line-up of the Ian Howe fleet at its previous Lincoln Road depot, now occupied by a prominent scrap metal enterprise.
By late 2011 the Lincoln Road site had become too small for Ian's growing inventory so a decision was made to move a little further west of the city to a new five-acre premises at Whenuapai.
The purpose-built office and workshop facility has a bright and breezy ambience which not too many years ago would have been totally at odds with the working environs one associated with the concrete pumping industry.
The company employs around ten staff at any given time, including mechanics, but generally everybody pitches in to work on whatever task is needing completion.
While Harriet multi-tasks in the office, carrying out the role of office manager, accountant and dispatcher (she currently occupies two desks, flitting between the two roles with ease), Ian is just as happy working on repairing equipment as he is out in the field operating a pump.
The couple's son Trent is currently in his final few months of high school and works whenever he possibly can in the business, doing anything from mechanical work to being out on the job pumping concrete.
It's easy for an outsider to see that this is a family business and your surname doesn't necessarily have to be Howe to be a part of the family.
Ian reckons you can't place too much importance on having the organisation working as a team. "Kind of like an extended family really," he says.
And he's not just paying lip-service to that premise either. It can be evidenced by stepping out to the well-appointed workshop, complete with hooded barbeque, ready and waiting for the next 'family' get-together.
Keeping the family safe at work is at the forefront of company thinking and a new training room is currently under construction, where everybody from the owners, to the newest employee will receive training on new equipment as it is introduced, along with revalidation of existing qualifications and certification.
Ian is quick to point out the importance of placing great store on health and safety. While taking a walk around the yard he talks of the potential dangers of working in an industry where aggregate is pumped at pressures of up to 130 bar.
As the science of concrete manufacture has changed over the past few decades, so have the mechanics of pumping it and Ian Howe Concrete Pumps has always been at the forefront of effecting change.
Back in the early 1990s, Ian had figured that traditional mechanical pumps operating on a system using cams and chains, required a lot of maintenance due to their inordinate number of component parts and that there had to be a better way of imparting the considerable amount of energy required to pump a product that weighs two tonnes per cubic metre (twice the weight of water).
His quest to find a more effective trailer-mounted pump led him to Australia where he found the answer in the form of hydraulic pumps which use technology that has now brought his business to a point where it solely operates hydraulic line-pumps which have a much greater pumping capacity and don't wear out as quickly.
To give an example of the extra output gained by using hydraulic pumps in the smaller range, a mechanical pump will pump around 19 cubic metres per hour while hydraulic models have an output of around 35-40 cubes per hour.
Friction created while pumping concrete also plays havoc with interior surfaces of pipe-work, so Ian is replacing all his existing pipes with new technology, a 'twin wall' line-system pipework.
The tungsten carbide lining, he says, reduces friction in the pipes and will increase their life by perhaps as much as eightfold.
A lot of hard yards have gone into building Ian Howe Concrete Pumps, a company that began as a 'one-man band' and now owns around twenty rigs including trucks and utes.
All the boom pumps are operated via radio remote and given that they're always operating in a hostile environment, they will sometimes malfunction.
When Ian couldn't find any technicians in Auckland able to repair the units, he figured out how to do the job himself and is now the resident radio-remote electronics tech.
Today, most of Ian Howe Concrete Pumps' work comes as a result of requests from corporate clients, although the company also operates on smaller residential jobs as well.
The company has pumped concrete on most of Auckland's infrastructure jobs, including the Victoria Park Tunnel project, the New Lynn rail trench, in which it pumped around 100 cubic metres per day for nearly 10 months, a recent large pour for a bus company in Ranui, west of Auckland and is, at the time of writing, working on the Waterview tunnel project.
The firm is also called upon from time to time to provide technical and logistics advice during the planning stages of larger or more difficult projects.
The company currently operates four 28-metre boom pumps, one 33-metre and one 36-metre unit and is about to add yet another boom pump to the fleet. Although a final decision is yet to be made as to what brand of truck it will be attached to, it will more than likely be equipped with a new-generation Putmeister pump and will sport a 42-metre, four-section boom.
There are ten other pumps in the fleet, including a high-rise pump and a number of trailer-mounted line and shotcrete pumps.
Now, just in case there is anyone out there thinking to themselves this could be a bit of a cushy number to get into, then perhaps you'd better think again — especially you're not keen on the prospect of throwing continual 12-13 hour days at your business.
Crews are often on the road at 3am in order to be on site in time for early pours and don't forget the job isn't over the moment the concrete stops flowing either!
Concrete pumps tend not to work too well unless they're meticulously cleaned and many an operator in a hurry to head off for the end of day's activities has been given a sharp reminder of the of the correlation between cleanliness and Godliness the following morning when the pump has refused to operate.
Writer's note: While taking the photos for this article, at the end of the working day
at the Whenuapai yard, a team member was seen spending a painstaking 45 minutes cleaning out his pump and making sure it was all good to go for his 2.30am start the following morning.
Ian Howe says the success of his business has been built on employing staff who have a good work ethic and by using top-of-the-line German pumping equipment.
"In a time-critical business like the concreting game you can't afford breakdowns and stuff-ups, you have to always bear in mind that once the concrete is in the hopper it's starting to set," says Howe.
For the latest reviews, subscribe to our Deals On Wheels magazine here.
Keep up to date in the industry by signing up to Deals on Wheels' free newsletter or liking us on Facebook.