Hibiscus Contractors
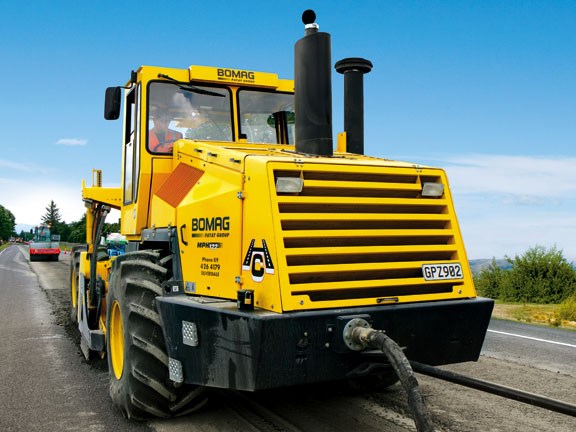
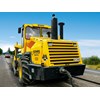
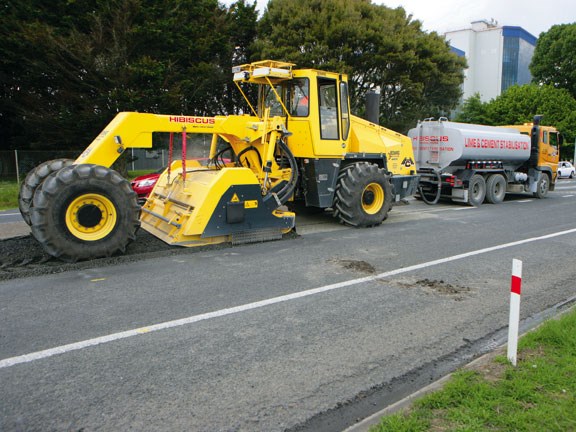
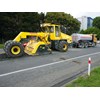
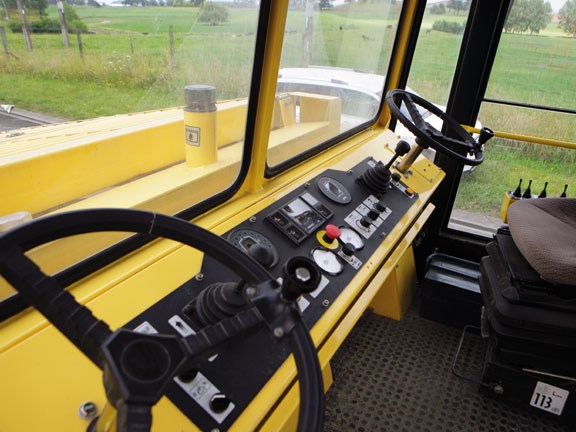
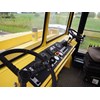
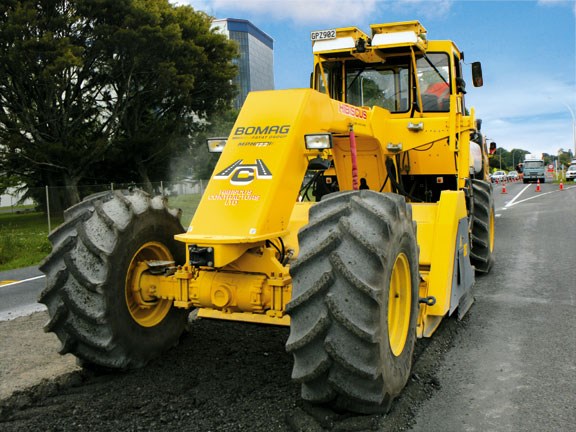
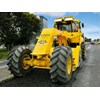
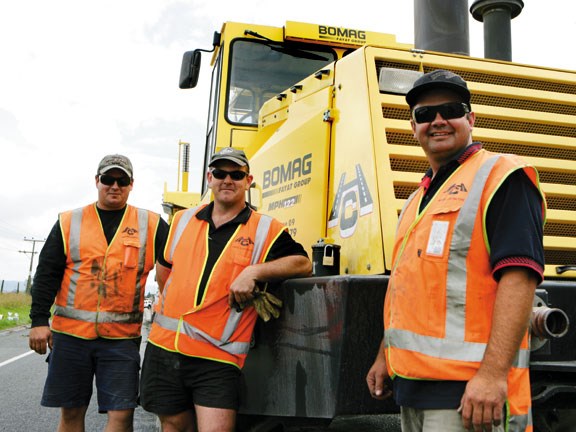
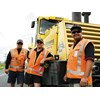
![]() |
![]() |
![]() |
![]() |
![]() |
It’s expensive to build a new road or even to renovate an existing one. Road builders must do the best they can with the base layer they have. This means limiting the use of new aggregate by stabilising the soil of a new road bed and recycling existing pavement as much as possible. But with a Bomag MPH122-2 road stabiliser and recycler, it’s all in a day’s work.
![]() |
Hibiscus Contractors
|
Motorists and transport operators who travel on roads under renovation may grudgingly accept the inconvenience that accompanies this necessary work.
However, very few will understand the focused logistical planning that goes into the process to keep the disruptions minimal, or the elegant solutions of the specialised equipment road builders use to make the process as sustainable and environmentally friendly as possible.
Civil construction company Hibiscus Contractors of Silverdale, Auckland, specialises in residential and commercial subdivisions and road construction, and is currently engaged in completing overlays on stretches of state highways in the Waikato as subcontractor for Fulton Hogan. Company owner Linden Bawden, operations manager Shaun Bawden, and machine operator Greg Hall explained to Deals on Wheels the difference between soil stabilisation, road renovation with recycled asphalt, and how the plant operates.
Linden says any land-based structure is only as strong as its foundation. This means soil is a critical element in determining the success of a project and understanding its engineering properties is important.
Construction and the necessity of improving the engineering properties of soil go hand in hand.
Engineers are seldom fortunate enough to build or renovate roads on soil that has ideal engineering properties, namely an optimal range of different sized particles that are well-drained, compacted and stabilised. Soil stabilisation is the process of maximising soil suitability for specific construction ends.
The modern era of soil stabilisation began when global shortages of petroleum and aggregates resources versus increased demand forced engineers to consider alternatives to the earlier conventional technique of replacing poor soils as building sites with shipped in aggregates that possessed more favourable engineering characteristics. Stabilisation can be done chemically or mechanically or both.
In chemical stabilisation, a construction vehicle spreads binder agents such as lime, fly ash, or cement on the proposed road bed. A road stabiliser then blends the soil, the binder agent, and water together. It is also fitted with a powered metal drum that has rows of mixing paddles or teeth.
The drum is lowered onto the ground and the teeth cut into the top surface of the soil with the agents spread on it. As the machine progresses, the hoed material is mixed with water in the chamber via a computer-controlled system. The water is provided by a water truck connected by hose to the stabiliser. This results in the right consistency mix. The mix is deposited from the mixing chamber back onto the road bed.
When appropriately designed and constructed, an asphalt road does not wear out. However, it must provide sufficient friction for car tyres to be safe so, due to wear and tear, it needs maintenance. To do this, the top layer of the road is removed and replaced. The newly overlaid road surface is a good-as-new pavement. The removed layer can be recycled so that only limited quantities of new resources are used.
A road recycler works exactly like a stabiliser, except that the paddle teeth need to be much stronger to be able to cut and pulverise the top surface off a paved road. In both applications the vehicle might need to make several passes over a stretch of road to achieve the desired outcome. As Hibiscus engages in new road construction as well as renovation, Linden says it makes sense that its plant will be versatile enough to do both jobs and can work on big and small projects with equally cost effective outcomes. In mid-November, Hibiscus Contractors took delivery of a Bomag MPH122-2 road stabiliser and recycler, bought from Porter Group. The machine is part of an expanding fleet and joins a Komatsu already at work.
Operator Greg Hall and his new machine 'hit the road running' and by mid-December 2012 the Bomag had already completed 150hrs-odd for Hibiscus, working on SH1 and SH29. Several features of the Bomag MPH122-2 impressed the men greatly.
The vehicle features a Tier-3-compliant, 482-horsepower Deutz V6 engine. It offers a 2400mm-wide universal rotor with tine-type teeth and a 500mm cutting depth. The rotor drive is an integrated hydrostatic type.
The multi-purpose rotor offers speeds able to be selected under load and matched perfectly to the requirements of any task. The variable mixing chamber is automatically adaptable to any cutting depth, irrespective of soil and material types. Thus, binder and soil are processed to a uniform texture resulting in low parts wear and optimised power consumption.
In recycling applications the machine is used to cut and pulverise old, damaged surfaces and road pavements. Here the complete road construction, including the bearing course, is treated. The pulverised material is then mixed with a binder such as cement in place and reused as a new bound bearing course. Specially designed additive systems for water, bitumen emulsion, and foam bitumen extend the versatility the MPH 122. Hibiscus' model uses only a water additive system.
"We're impressed with its power. We make fewer runs, the machine can be used for a wide diversity of jobs, and the manoeuvring ability, the result of the combination of articulated and rear axle steering, is awesome. Having the luxuries of an enclosed cab with all the modern conveniences such as air conditioning and a stereo system is great," says Linden.
"We particularly like the computer-controlled water injection system, which enables excellent quality control. Overall, the powerful rotor and travel drives ensure consistent mixing results and efficiency."
Greg smiles from ear to ear when he talks about his new plant.
"I love the comfort, it is a pleasure to operate," he says. Greg explains that visibility to the entire work area and nimbleness of the machine also greatly reduces work stress and fatigue, while maintaining the teeth on the drum is easy and problem-free.
Linden says Hibiscus' relationship with Porter Group goes back two decades and when the team decided to add a stabiliser and recycler to the fleet, it approached the company for its trusted advice about the right product at the right price.
"Porter's support has been excellent. The Porter Group product manager, Scott Turner, travelled to Germany for training and in turn trained us how to operate it and get the best from it. We had a few teething problems right at the beginning but Scotty was on- site inside an hour to fixing the issue, which turned out to be fairly simple and downtime was less than three-hours," he says.
"We are in the process of establishing how it is running, feeling our way with cost comparisons. It is a totally new experience to us, but so far it has proved ideal for big jobs, easy to transport, nimble on the work site, and a pleasure to operate."
Who is Hibiscus Contractors?
Established in 1980 on the North Shore, Hibiscus Contractors' service areas are road building, residential and commercial subdivisions, lime and cement stabilisation, lime drying, and civil construction. Over the course of the decades, it has been the civil contractor in the development of many major projects including the Maygrove subdivision in Orewa; a portion of the Pauanui development in Pauanui; Whangaparaoa College in Whangaparaoa; and numerous road reconstruction contracts for the Hauraki District Council, the Kaipara District Council, North Shore City Council, Rodney District Council, and Thames Coromandel District Council.
Hibiscus Contractors was also the main contractor on the construction of the Gulf Harbour development, including all roading and associated works, the marina, and building the canal. The work also included building the International Golf Course which was the venue for the World Cup of Golf in 1998. The company works for a wide variety of upper North Island clients, ranging from private developers to city and district councils and acts as subcontractor for a number of iconic builders such as Fulton Hogan, Transfield Services and Higgins.
Feel free to make a comment or ask us a question about this story on the Deals On Wheels page.
For the latest reviews, subscribe to our Deals On Wheels magazine here.
Keep up to date in the industry by signing up to Deals on Wheels' free newsletter or liking us on Facebook.